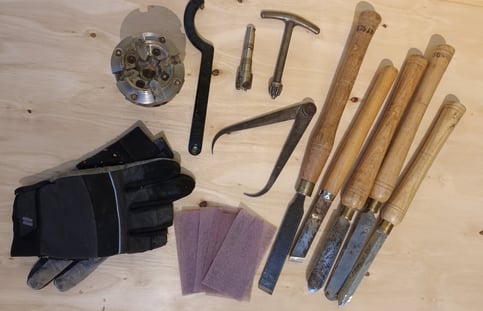
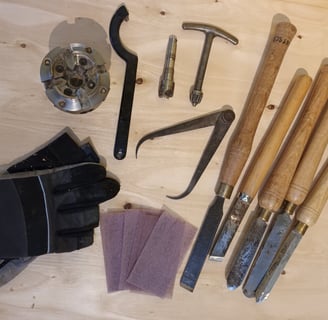
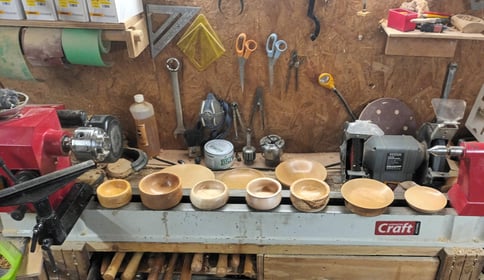
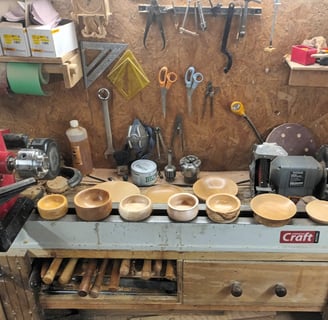
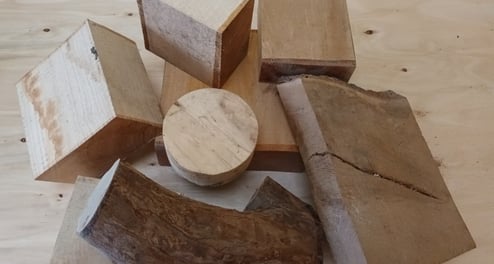
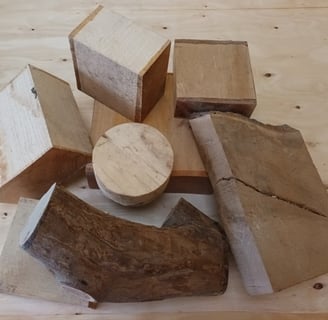
I have been wood turning since lockdown, learning about how the wood reacts to it's environment and how I work with it. I have also tailored my tools and working methods to suit my own priorities, which makes the way that I work, and the items that I make, unique.
Living on the edge of the National Forest allows me to source my timber directly from one of the people who help manage the woodland. This means that I can choose my pieces personally, and I often go for the ones that nobody else wants, because they tend to have knots or warps in them. This is part of the uniqueness of wood - I like to bring out the beauty of what others see as faults. Sometimes I will choose a piece of wood for the grain pattern, because a blemish free piece with interesting markings makes for a stunning item.
Every piece is unique, because the nature of the material makes it impossible to make two the same. I am passionate about the process of taking a rough piece of timber and making something tactile and useful, as well as saving it to serve another purpose, because each piece has its own beauty.
Once the piece of wood is on the lathe, I rough turn the outside, taking into account any imperfections that I want to remove or enhance. This will dictate the size and shape of the finished item, as well as the size of the pile of shavings.
When I am happy with how the bowl looks, I use planing cuts to smooth the surface of the wood, before sanding with successive grades of abrasive cloth up to 600 grit, and then finish it with several coats of wax.
More shavings are created when I turn the inside of the bowl. The finishing process for the inside of the bowl is exactly the same as for the outside.